Someone suggested I put up some photos showing how I make scales - Jamie had already shown his manual method so I thought it would make a comparison to show my use of powered tools.
The razor was sent to me by Magnus - it had already been cut down at the heel and toe from the look of it, and Magnus wanted something a bif different.
I started by drawing an outline of the razor designing the scales and cutting the template - here we see the template and black horn that will be used.
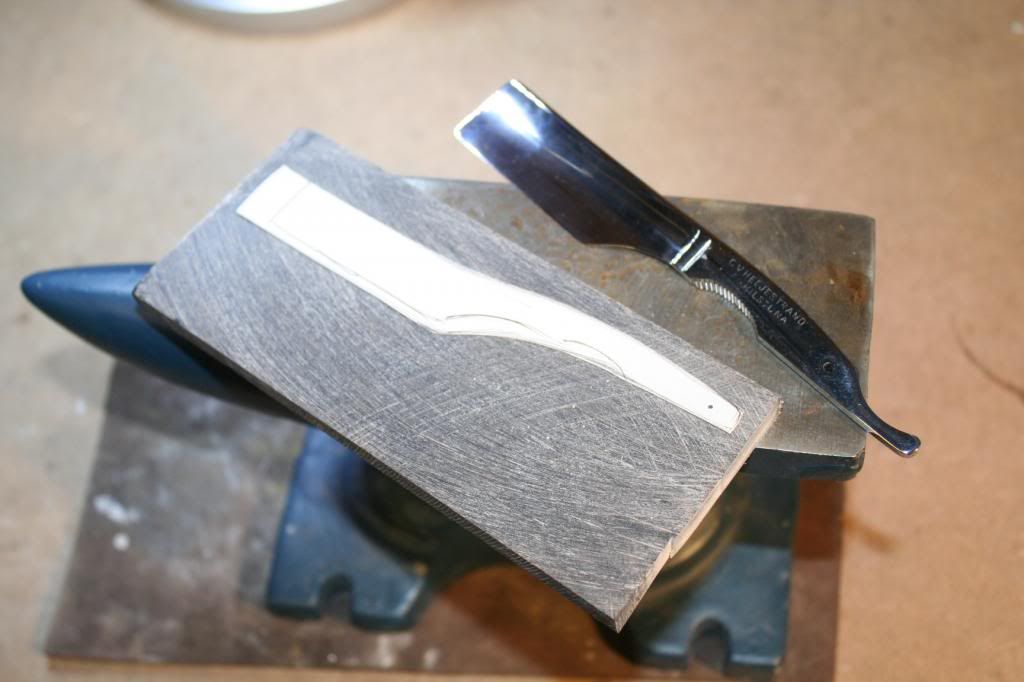
At this stage the horn is about 7.5mm thick so I want to take it down to about 3mm eventually. The slab is mounted onto a paddle with double sided tape and put through my drum sander which is attached to a drill press. I aslo have a 'Luthiers Friend attached to the press - this enabled very accurate thcknessing as the upright can be moved towards the drum in tiny increments.
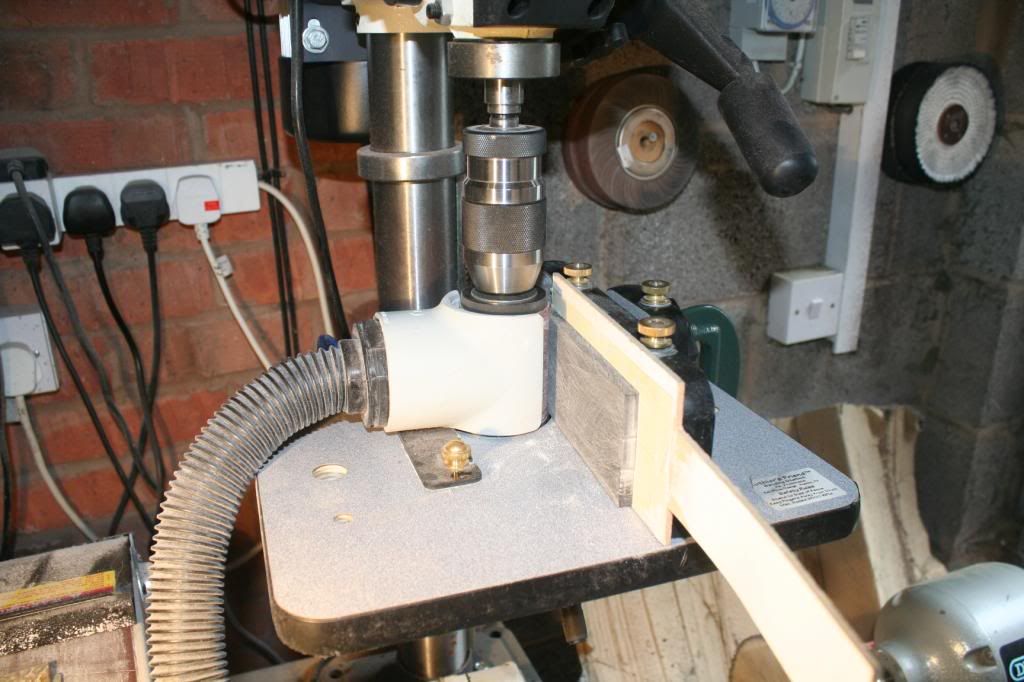
At this stage the blanc is down to sbout 5mm so I switch to a lower (about 200 grit) paper.
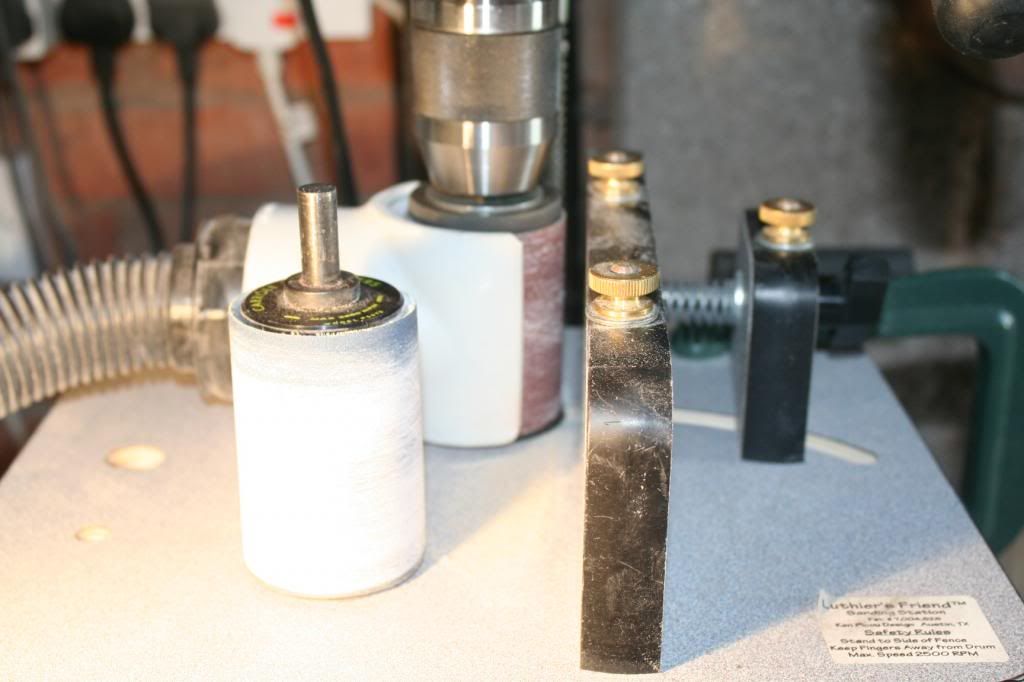
Once I'm down to about 3mm the blank is halved lengthways, taped together and than masking tape applied to the front so that the outline can be drawn from the template. At this stage I've already decided front and back based on how the grain runs. With scales if there's any curve in the grain you want it upwards - well I do anyway.
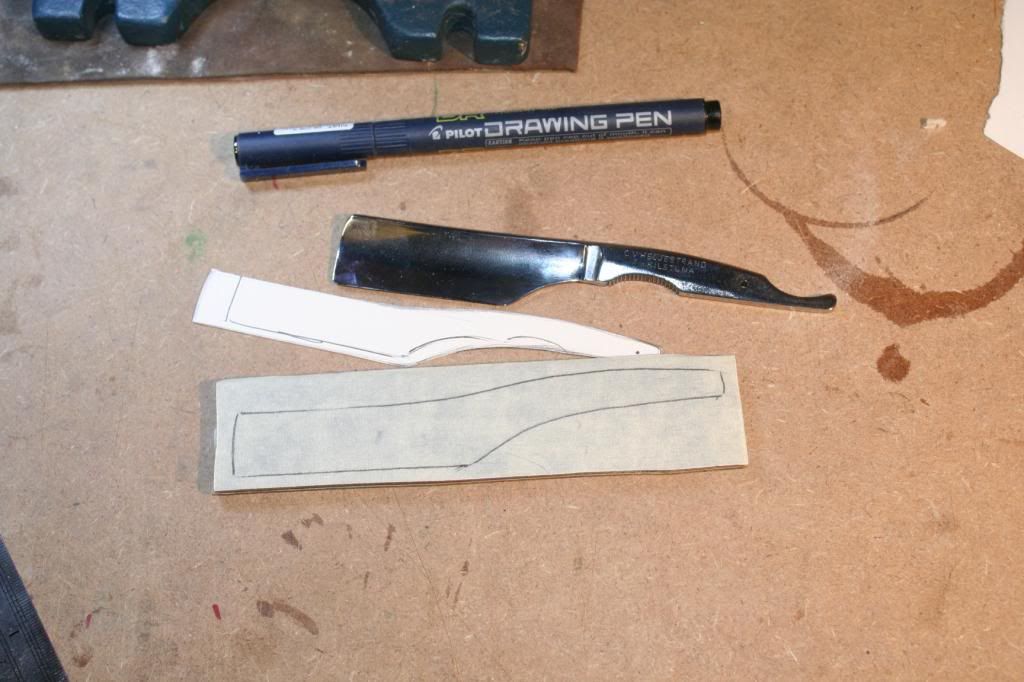
Rough cut on the scroll saw.
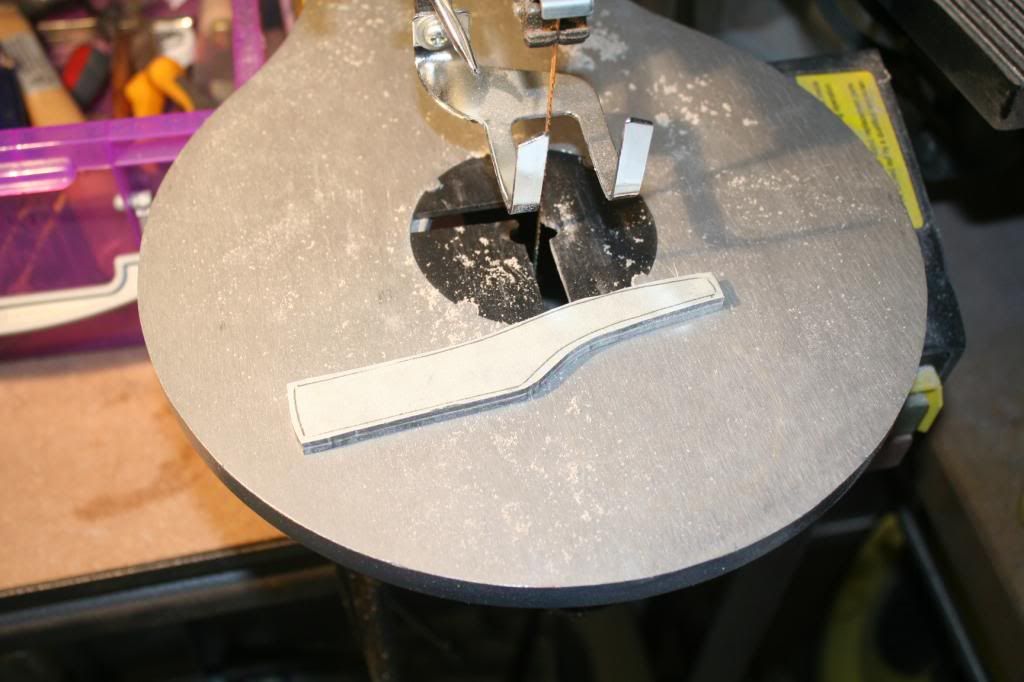
Next it was refining the shape on the belt sander - this is where I start hand sanding.
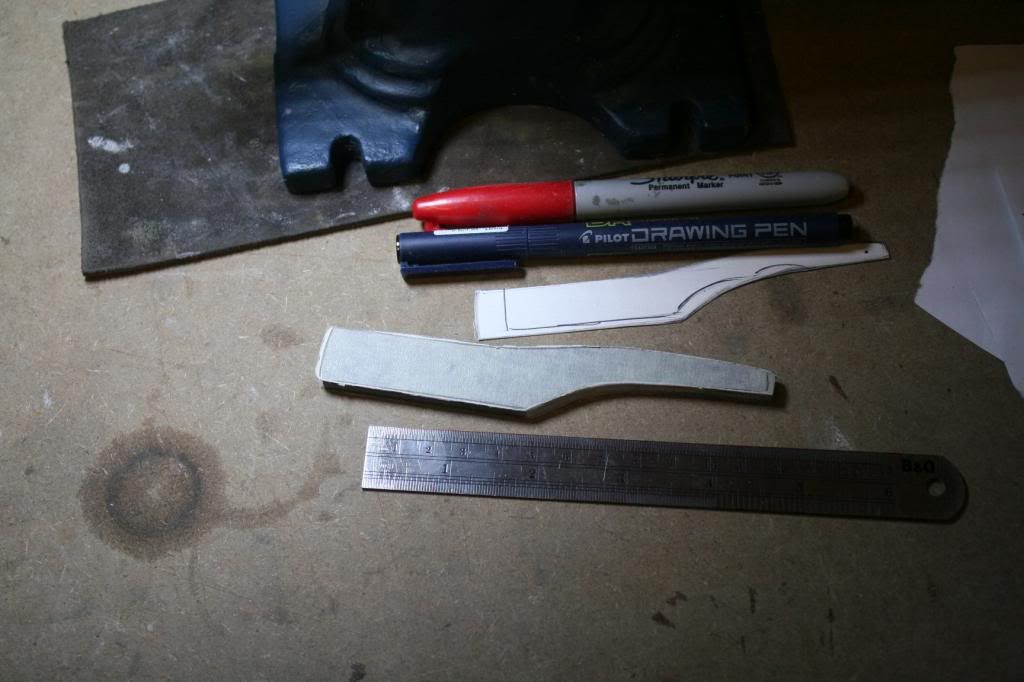
To be continued.
Hand sanding begins with 180 grit through 280, 400, 600. 800 and 1000. This is after 1000
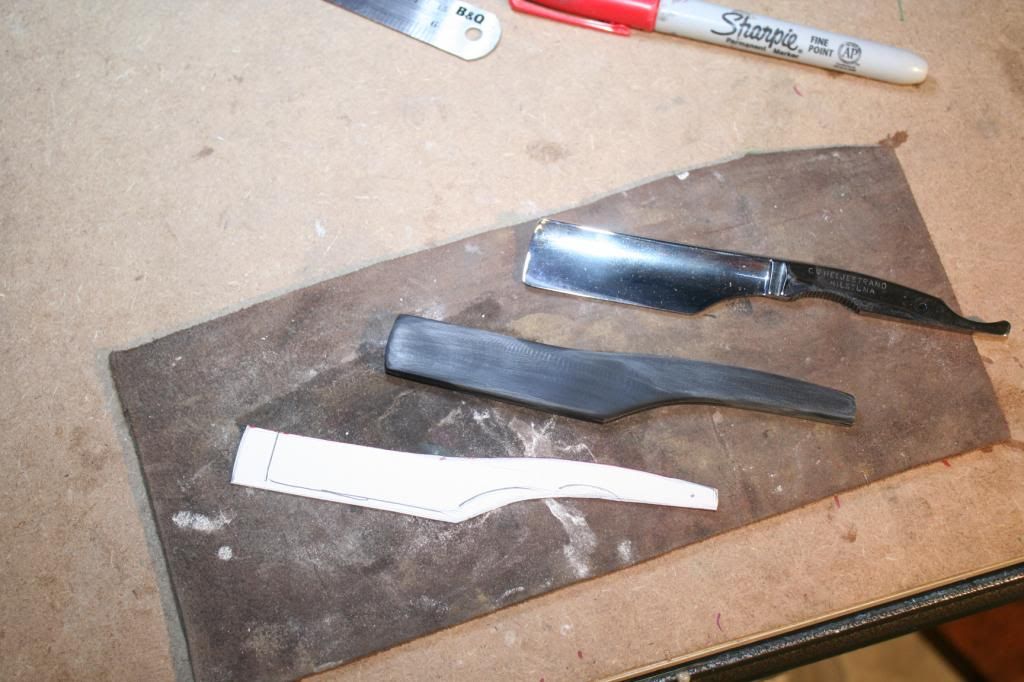
After that, I use a buffing machine with a produvt called Vonax. You will see I drilled the pivot and wedge pin holes - this is done accurately with the blade in place so that I know where the wedge will be.

Next is shaping the wedge - Magnus had sent a piece of Musk Ox Horn. I came up with the idea of using a door wedge to get an accurate shape - doing this by eye is very hit and miss but using the wedge and drum sander is very accurate.
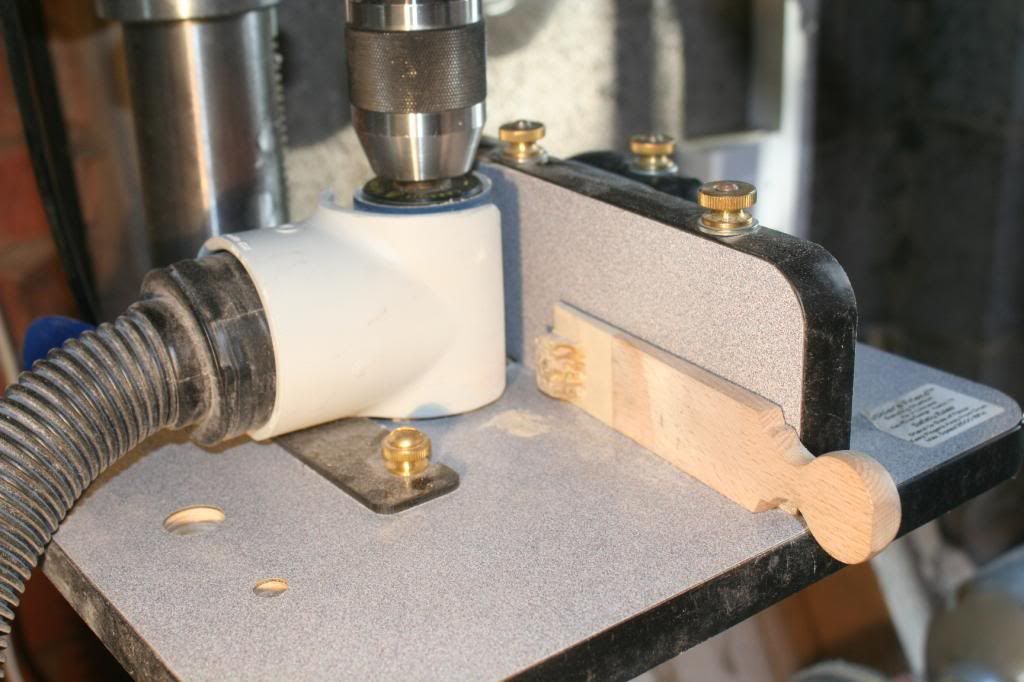
The razor was sent to me by Magnus - it had already been cut down at the heel and toe from the look of it, and Magnus wanted something a bif different.
I started by drawing an outline of the razor designing the scales and cutting the template - here we see the template and black horn that will be used.
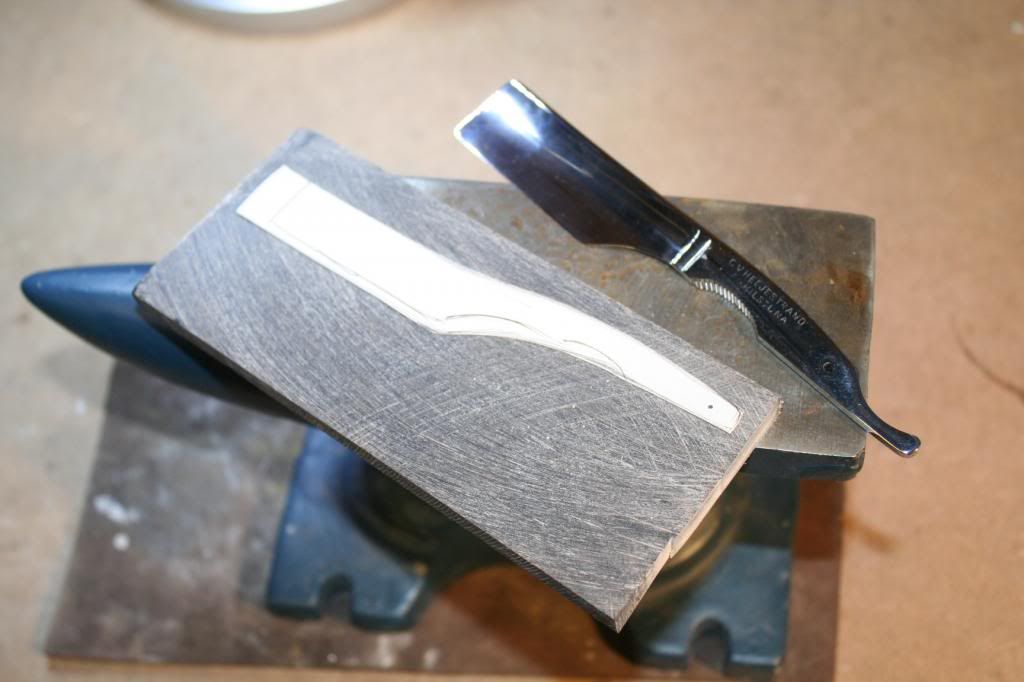
At this stage the horn is about 7.5mm thick so I want to take it down to about 3mm eventually. The slab is mounted onto a paddle with double sided tape and put through my drum sander which is attached to a drill press. I aslo have a 'Luthiers Friend attached to the press - this enabled very accurate thcknessing as the upright can be moved towards the drum in tiny increments.
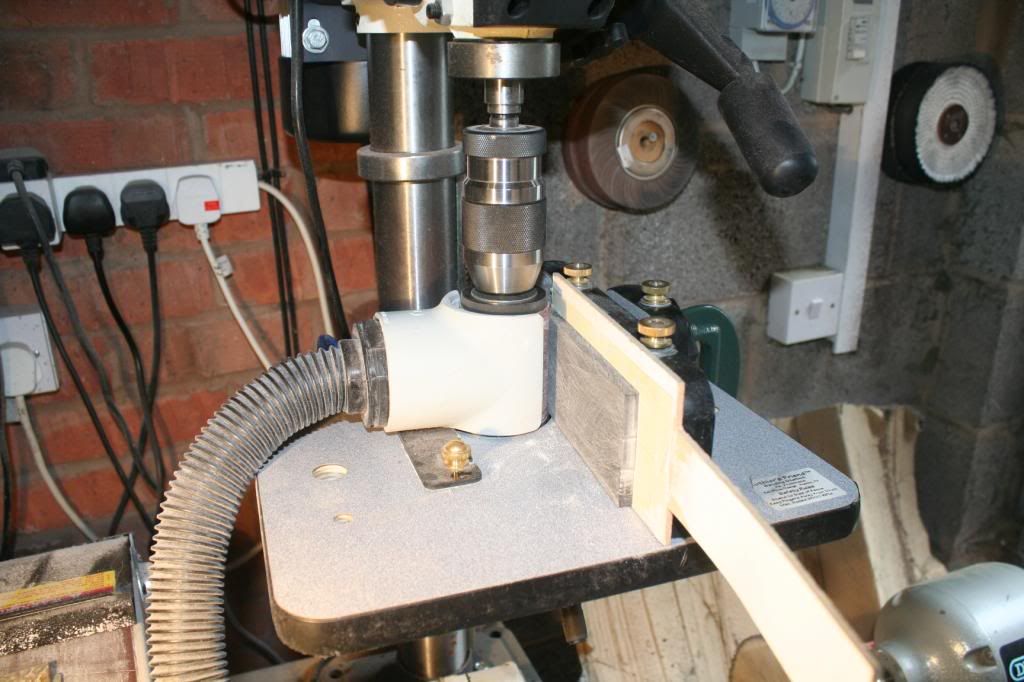
At this stage the blanc is down to sbout 5mm so I switch to a lower (about 200 grit) paper.
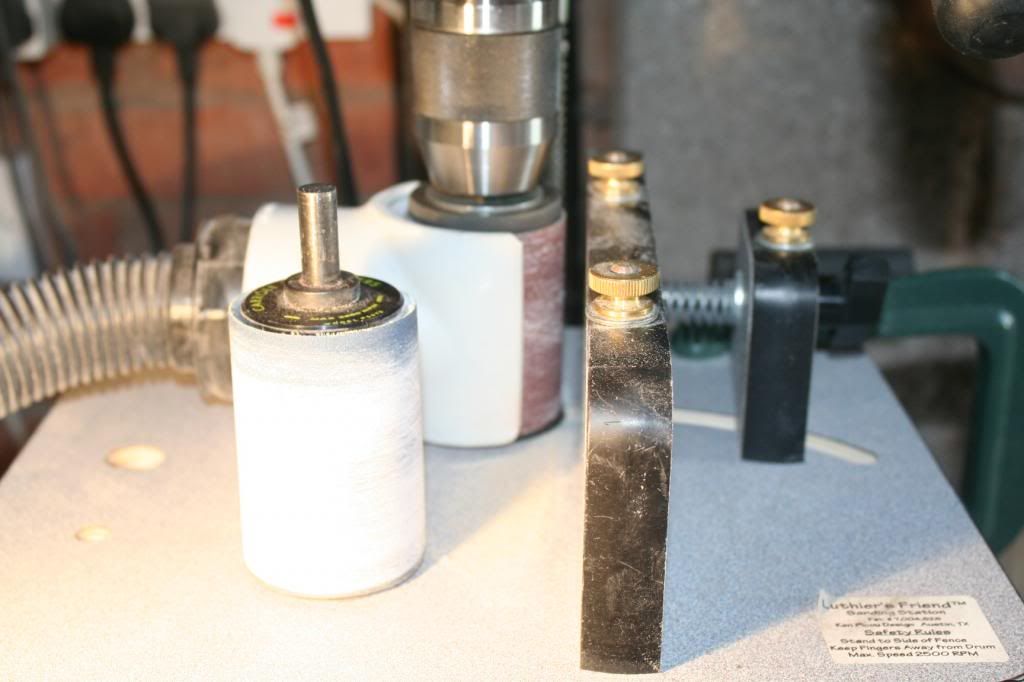
Once I'm down to about 3mm the blank is halved lengthways, taped together and than masking tape applied to the front so that the outline can be drawn from the template. At this stage I've already decided front and back based on how the grain runs. With scales if there's any curve in the grain you want it upwards - well I do anyway.
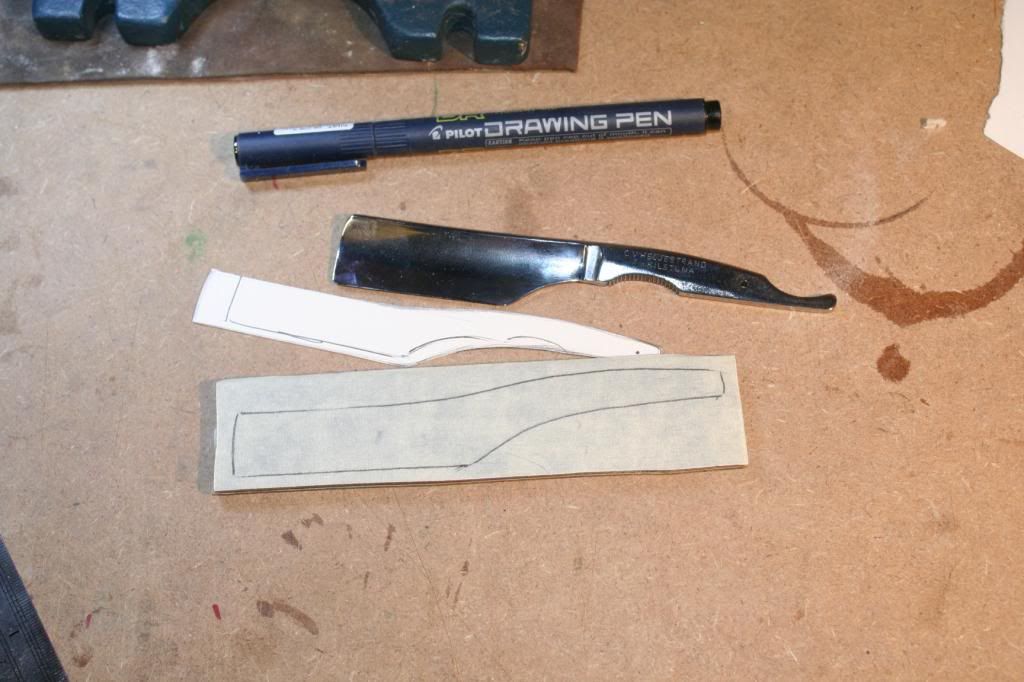
Rough cut on the scroll saw.
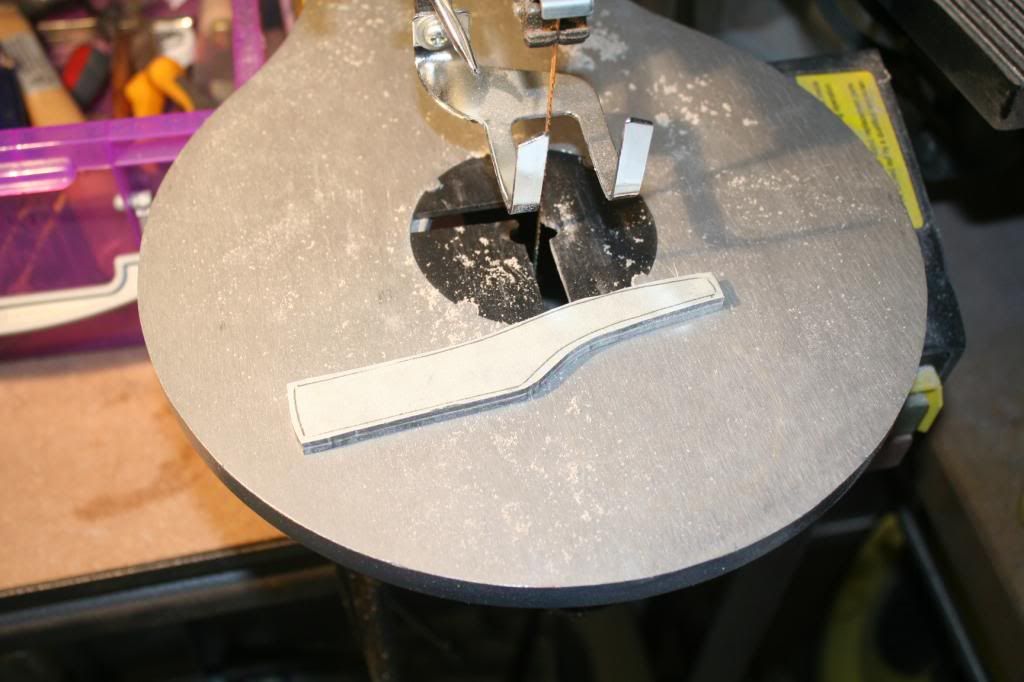
Next it was refining the shape on the belt sander - this is where I start hand sanding.
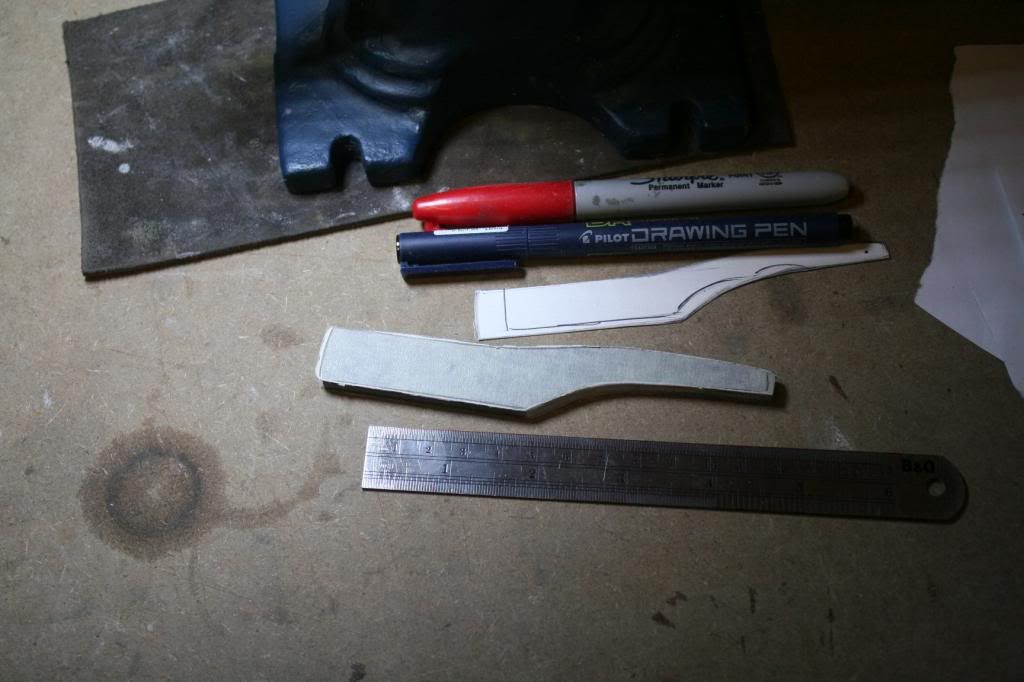
To be continued.
Hand sanding begins with 180 grit through 280, 400, 600. 800 and 1000. This is after 1000
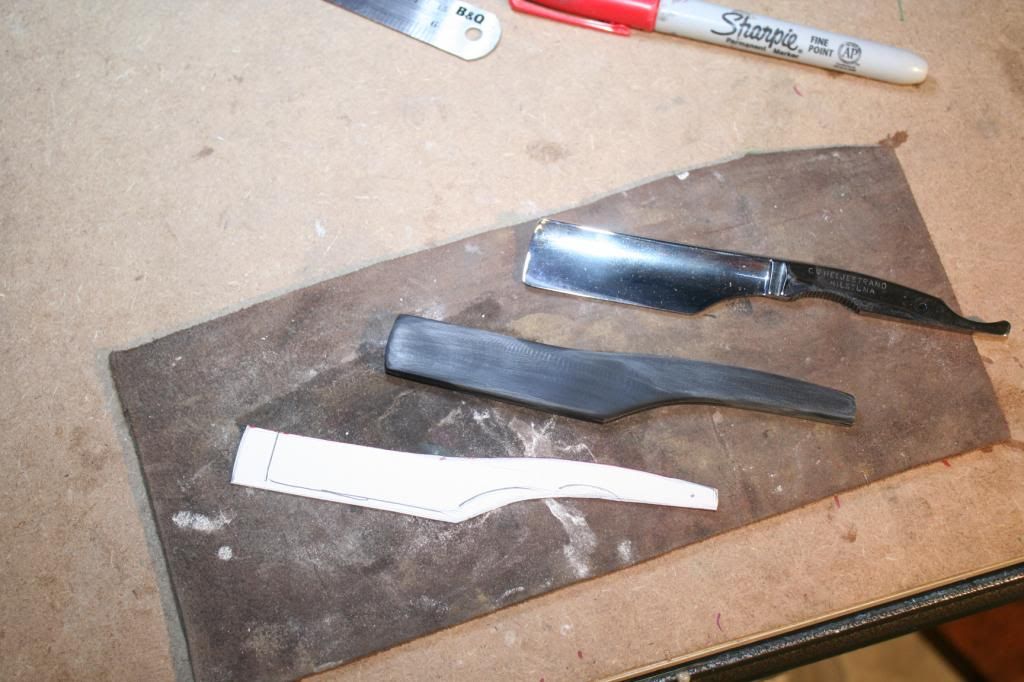
After that, I use a buffing machine with a produvt called Vonax. You will see I drilled the pivot and wedge pin holes - this is done accurately with the blade in place so that I know where the wedge will be.

Next is shaping the wedge - Magnus had sent a piece of Musk Ox Horn. I came up with the idea of using a door wedge to get an accurate shape - doing this by eye is very hit and miss but using the wedge and drum sander is very accurate.
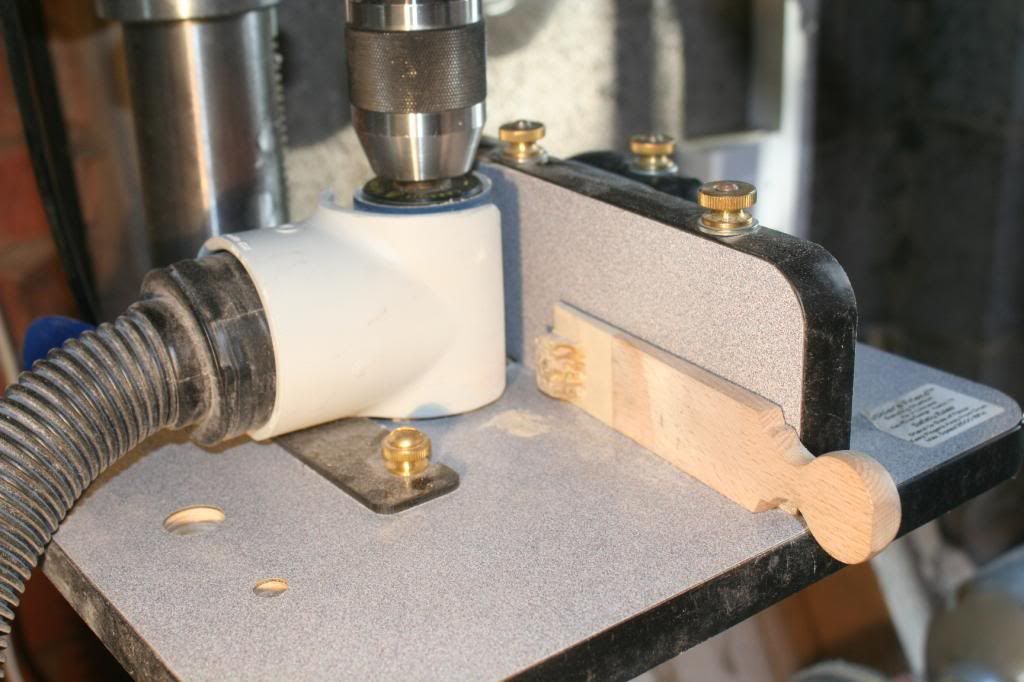